Silicone Injection Molding Manufacturers: Innovations in Electronics and Medical Supplies
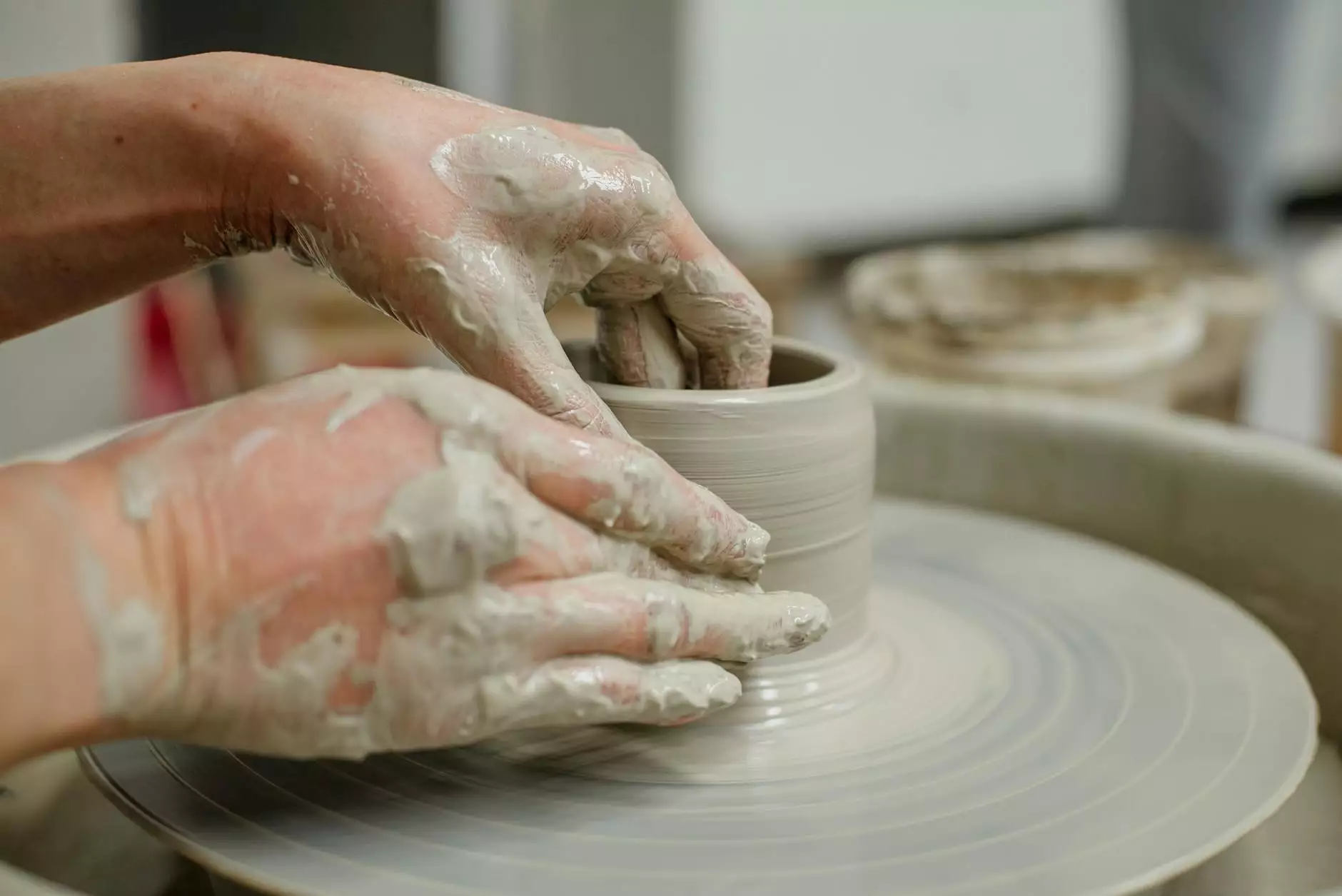
The industry of silicone injection molding has seen tremendous growth and innovation in recent years. As a cornerstone in the production of various products, silicone injection molding offers unmatched versatility, durability, and flexibility. In this comprehensive guide, we delve deep into the realm of silicone injection molding manufacturers and their significant contributions to the electronics and medical supplies sectors. This article aims to provide valuable insights that can help businesses and individuals understand the importance and advantages of silicone molding.
The Process of Silicone Injection Molding
At its core, silicone injection molding is a process that involves injecting liquid silicone rubber (LSR) into a mold to create precise, durable components. This manufacturing technique is widely favored for its ability to produce complex parts with intricate designs. Here are some key steps involved in the process:
- Material Preparation: Liquid silicone rubber is prepared by mixing silicone polymers with additives that enhance the material's properties.
- Mold Design: High-quality molds are designed using advanced CAD software to ensure precision and meet specific product requirements.
- Injection: The prepared silicone material is heated and injected into the mold at high pressure, ensuring that every detail is captured.
- Curing: The injected silicone undergoes a curing process, which solidifies the product, giving it the desired strength and stability.
- Demolding: After curing, the mold is opened, and the finished components are ejected, ready for finishing processes.
Benefits of Silicone Injection Molding
Silicone injection molding is revolutionizing manufacturing in both the electronics and medical sectors. Below are some significant benefits that make it a preferred choice among silicone injection molding manufacturers:
- High Precision: The injection molding process ensures tight tolerances and high repeatability, creating parts that meet exact specifications.
- Durability: Silicone materials are resistant to extreme temperatures, UV light, and chemicals, making them ideal for various applications.
- Design Flexibility: Manufacturers can create complex shapes and designs that are not possible with traditional manufacturing methods.
- Cost-Effectiveness: While the initial setup costs may be higher, silicone injection molding can reduce long-term production costs due to its efficiency and speed.
- Biocompatibility: Medical-grade silicone is safe for prolonged human contact, making it the preferred choice for medical device manufacturers.
Applications in Electronics
In the electronics industry, silicone injection molding has become indispensable. Here’s how silicone plays a critical role:
Seals and Gaskets
Seals and gaskets made from silicone provide excellent insulation and sealing properties, ensuring that electronics are protected from moisture, dust, and other contaminants. They are widely used in:
- Smartphones
- Home appliances
- Computers and peripherals
Keypads and Buttons
Silicone rubber keypads are popular due to their tactile feel and durability. They are commonly used in:
- Remote controls
- Medical devices
- Consumer electronics
Insulation for Wiring
Silicone’s electrical insulating properties make it an ideal choice for coating wires and cables, ensuring safety and effectiveness in electronic devices.
Applications in Medical Supplies
The medical sector demands high standards of quality and safety, and silicone injection molding plays a pivotal role in meeting these needs. Some of the key applications include:
Medical Devices
Silicone is extensively used in the production of medical devices such as:
- Catheters
- Respiratory masks
- Implants
Surgical Supplies
Surgical masks, gloves, and other supplies manufactured from silicone are preferred for their biocompatibility and resistance to bacteria, which are essential for maintaining hygiene during medical procedures.
Drug Delivery Systems
Silicone’s flexibility and durability make it ideal for various drug delivery systems, ensuring that medications are administered safely and effectively.
Choosing the Right Silicone Injection Molding Manufacturer
When selecting a silicone injection molding manufacturer, it's crucial to consider several factors that can significantly impact the quality and success of your project:
Experience and Expertise
Look for manufacturers with a proven track record in the industry. Experienced companies understand the nuances of working with silicone materials and can offer valuable insights throughout the process.
Quality Assurance
Ensure that the manufacturer follows stringent quality control measures. Certifications such as ISO 9001 and ISO 13485 indicate adherence to high manufacturing standards.
Customization Capabilities
The ability to customize molds and designs is essential for creating unique products tailored to specific applications. Choose a manufacturer who can accommodate your design requirements.
Technical Support and Communication
Effective communication is key to successful collaboration. Your chosen manufacturer should offer excellent technical support throughout the project lifecycle.
Future Trends in Silicone Injection Molding
As technology advances, the field of silicone injection molding is evolving rapidly. Some trends to watch for include:
Enhanced Materials
New formulations of silicone that enhance properties such as conductivity and thermal resistance are being developed, expanding the potential applications in various industries.
4D Printing Integration
The integration of silicone injection molding with emerging technologies like 4D printing could lead to innovations in product design that adapt and change over time.
Automation and Industry 4.0
With the advent of Industry 4.0, manufacturers are increasingly adopting automation technologies that enhance efficiency and reduce human error in the injection molding process.
Conclusion
In summary, silicone injection molding manufacturers play a critical role in the advancement of products in both the electronics and medical supply sectors. With their unique properties and versatility, silicone materials are paving the way for innovative solutions that meet the demands of modern industries. By understanding the benefits and applications of silicone injection molding, businesses can make informed decisions that drive growth and success.
For organizations seeking reliable and experienced silicone injection molding partners, companies like Nolato.com exemplify excellence in providing high-quality, precision-engineered silicone solutions tailored to specific industry needs.