Business in Metal Fabrication - Boosting Success with a Plastic Injection Manufacturer
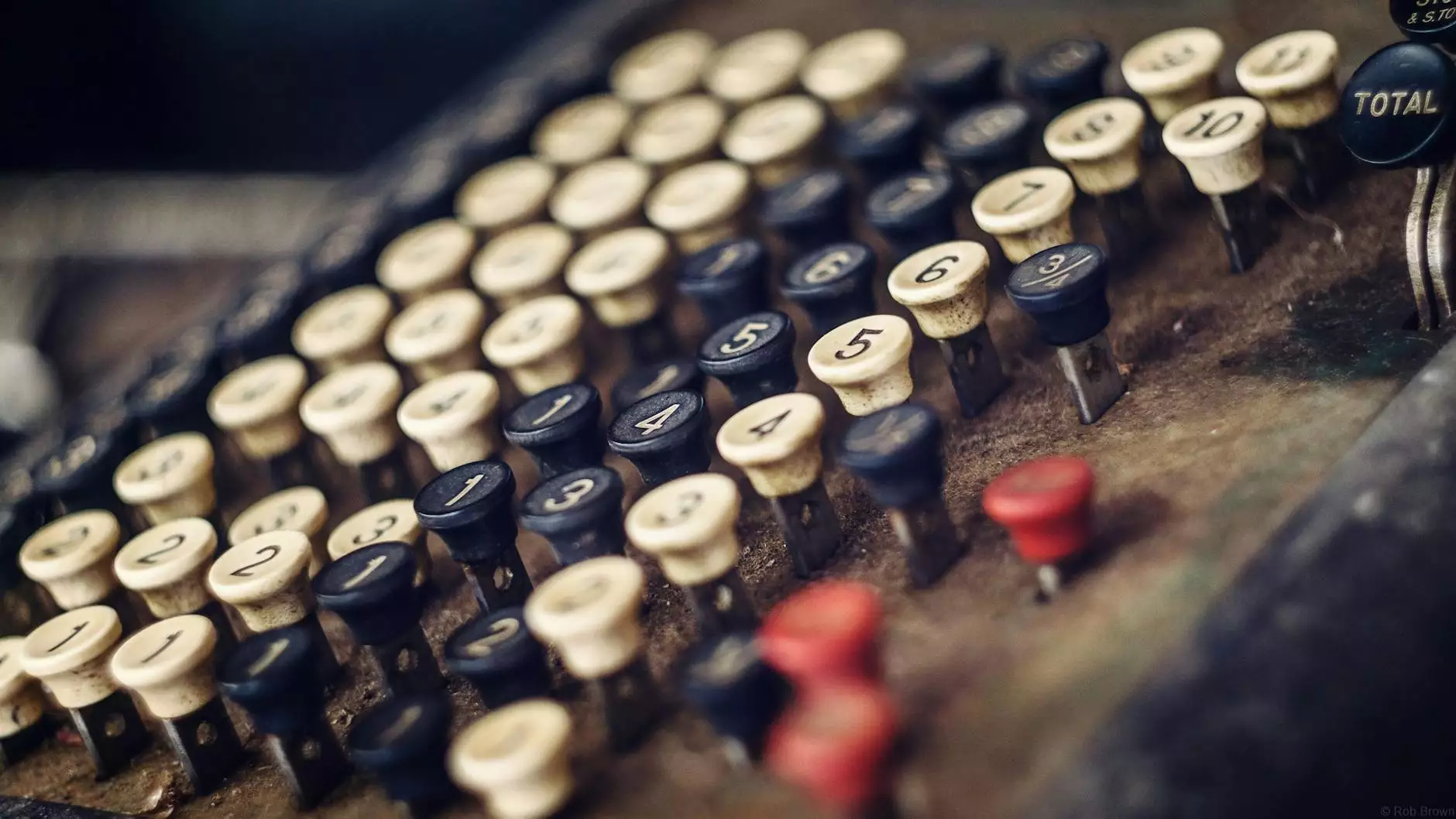
Introduction
Welcome to the world of metal fabrication and the endless possibilities it brings. In this rapidly evolving industry, staying ahead of the competition is crucial for success. To amplify your business potential and unlock new avenues, it's essential to explore strategic partnerships. One such collaboration that promises exceptional outcomes is partnering with a renowned plastic injection manufacturer. Discover how this collaboration can revolutionize your metal fabrication business.
The Role of a Plastic Injection Manufacturer
A plastic injection manufacturer plays a pivotal role in delivering high-quality and precise plastic components that complement your metal fabrication business. With advanced technology and expertise in molding plastic materials, a reliable manufacturer can fulfill your specific design requirements while meeting stringent quality standards.
Benefits of Partnering with a Plastic Injection Manufacturer
By leveraging the expertise of a plastic injection manufacturer, metal fabricators unlock several advantages that enhance their overall business operations:
1. Expanded Product Offerings
Collaborating with a plastic injection manufacturer opens new doors for diversifying your product range. By incorporating plastic components alongside metal parts, you can offer a more comprehensive solution to your customers. This expands your customer base and establishes your business as a one-stop destination for various manufacturing needs.
2. Enhanced Design Flexibility
Plastic injection molding offers unparalleled design flexibility. By working with a manufacturer proficient in this technology, you can create intricate shapes, complex geometries, and customized designs that meet the unique requirements of your customers. This brings your creativity to life and offers a competitive edge in the market.
3. Improved Product Functionality
Plastic components can enhance the functionality and endurance of your products. With the ability to integrate multiple functions within a single plastic piece, you can optimize designs for specific applications, improving performance and durability. This allows you to tailor your products to meet the ever-evolving needs of your clients.
4. Cost-Effective Solutions
Partnering with a plastic injection manufacturer offers cost-effective solutions in various aspects. The efficiency of plastic injection molding reduces material waste, resulting in lower production costs. Additionally, a reliable manufacturer ensures consistent quality, reducing the need for rework or product returns. These factors contribute to long-term cost savings for your business.
5. Streamlined Supply Chain
Collaborating with a plastic injection manufacturer establishes a simplified and streamlined supply chain. By leveraging their expertise in material sourcing and production, you can optimize inventory management and reduce lead times. This enables you to respond quickly to market demands, strengthening your business agility.
The Process of Plastic Injection Manufacturing
Now that we understand the benefits of partnering with a plastic injection manufacturer, let's dive into the process and gain insights into the intricate workings that yield remarkable results.
1. Design and Prototyping
It all begins with a detailed design and prototyping phase. Your manufacturer will work closely with you to bring your ideas to life. Utilizing advanced CAD software and their expertise in molding techniques, they will ensure that the design is optimized for efficient manufacturing.
2. Mold Creation
Once the design is finalized, the next step is creating the mold. Skilled toolmakers will meticulously craft the mold, considering factors like material selection, design complexity, and production volume. The mold will serve as a blueprint for the production of plastic components.
3. Material Selection
Choosing the right material is crucial for the success of your plastic components. Your plastic injection manufacturer will leverage their extensive knowledge and experience to recommend materials that align with your product requirements, whether it's durability, flexibility, or resistance to specific environmental conditions.
4. Injection Molding
The heart of the process lies in injection molding. Using the mold as a template, molten plastic is injected into the mold cavity under high pressure. This ensures the plastic takes the desired shape and conforms to the intricate details of the mold. The mold then undergoes cooling and solidification, allowing the plastic component to set perfectly.
5. Post-Processing and Quality Assurance
After the plastic components are formed, post-processing steps are carried out such as trimming excess material, applying surface finishes, and inspecting for defects. A reliable plastic injection manufacturer prioritizes quality assurance at every step, employing rigorous testing methodologies to deliver flawless components.
Tips for Maximizing the Impact of a Plastic Injection Manufacturer Partnership
To make the most of your collaboration with a plastic injection manufacturer, consider implementing the following tips:
1. Effective Communication
Clear and consistent communication is key when working with a plastic injection manufacturer. Discuss your design specifications, quality standards, and production timelines in detail. By maintaining open lines of communication, you can ensure a smoother manufacturing process and achieve the desired outcome.
2. Embrace Design for Manufacturing (DFM)
Collaborate with your manufacturer during the design phase by embracing Design for Manufacturing (DFM) principles. DFM involves designing parts that are optimized for efficient manufacturing, reducing costs, and ensuring ease of assembly. By incorporating DFM practices, you can streamline prototyping, production, and assembly processes.
3. Regular Collaboration and Feedback
Regularly collaborate with your plastic injection manufacturer throughout the production process. Seek their expertise and provide timely feedback. This iterative approach fosters continuous improvement and enables you to address any challenges or modifications required promptly.
4. Emphasize Quality Control
Quality control should be a top priority for both your business and the plastic injection manufacturer. Establish clear quality standards and implement robust inspection processes. By ensuring consistent quality, you enhance customer satisfaction and mitigate the risk of product defects or failures.
5. Explore Value-Added Services
Many plastic injection manufacturers offer value-added services such as assembly, packaging, and logistics support. Explore these services to streamline your post-production processes and enhance overall efficiency.
Conclusion
The collaboration between a metal fabrication business and a plastic injection manufacturer holds immense potential for growth and innovation. By leveraging their expertise, you can diversify your product range, enhance design flexibility, and deliver cost-effective solutions to your customers. Remember to communicate effectively, embrace Design for Manufacturing principles, emphasize quality control, and explore value-added services. Together, let's pave the path to success and outperform your competitors in this dynamic industry.